
It is modern communication technologies that have allowed unicorns to make a comeback. This collection was made by selecting the best creations from the Cults 3D print model library. All these STL files are easily 3D printable, so just download them, fire up your 3D printer and choose the color of your choice! Pink is obviously appropriate when it comes to unicorns, but you can think outside the box and create less usual unicorns in black or green. The expert team at Fathom has identified the most common pitfalls and guarantees that this STL Guideline document will save you time and ensure that your 3D printed parts accurately represent your idea.Check out our selection of the best 3D printer files for unicorn 3D printing. Our engineers are able to address the most common mistakes and potential errors with STL file preparation, as even the most popular CAD packages can pose difficulties during STL file export. Working with Fathom provides immediate and comprehensive access to the most relevant equipment and experience in advanced manufacturing, engineering, and prototyping.
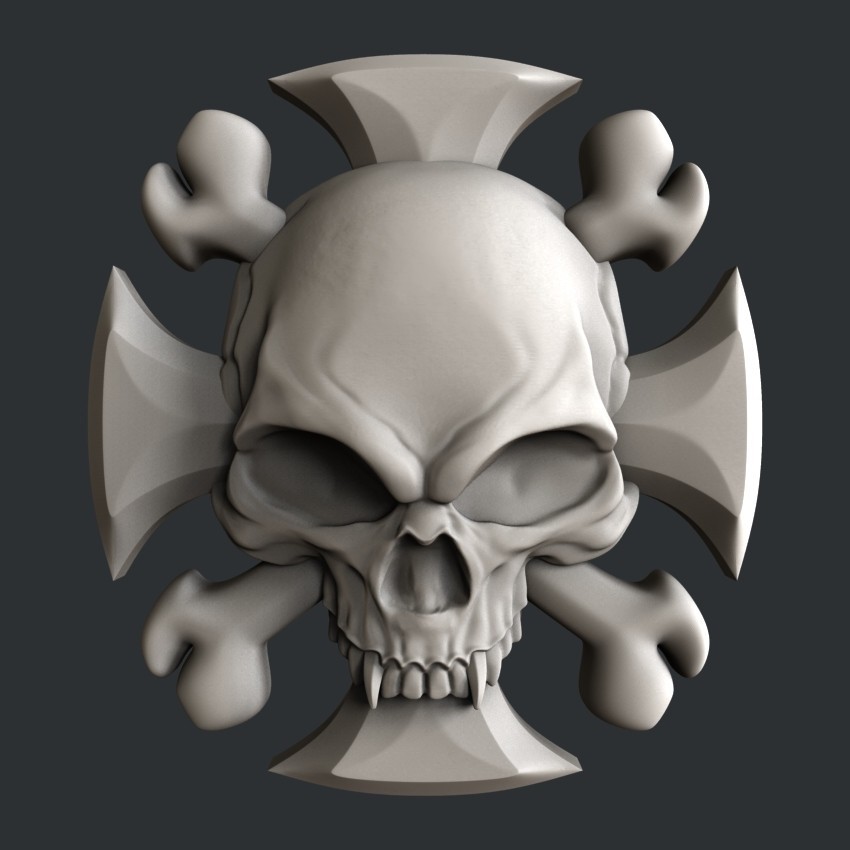
We recommend combining the bodies into a single solid before exporting into an STL. Intersecting faces usually lead to failures since the software doesn’t recognize which areas are inside or outside of the model. Overlapping & Intersecting Triangles / / Overlapping and intersecting triangles may produce areas too small to print. Solving any issues with your models in the native CAD software tends to have better results. We recommend removing noise shells for cleaner contours. Unwanted meshes and noise shells are typically created in error during an STL export. Multiple Shells / / Typically, it’s ideal for your STL to be made of one shell body for printing. It may be necessary to edit or re-export of the original 3D CAD file. This is sometimes an easy fix within the STL, but that is not always the case. Holes / / Missing triangles from a region prevents a closed mesh. Adding thickness or clearance where needed can sometimes help solve faulty edges. This requires STL repair and we recommend re-modeling the areas where the boundary edges were detected in the native CAD software. Many times, bad edges that are very close to one another may be stitched together to close the mesh.
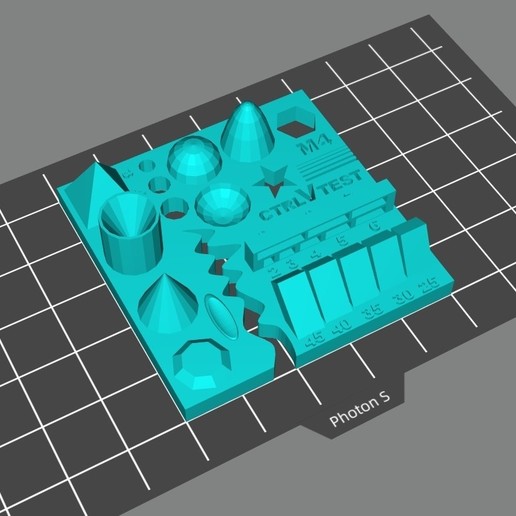
Simple STL editing software will enable you to flip the direction of the normal to correct the issues.īad Edges / / The edge of a triangle is not adjacent to another triangle edge. Because of this, slicing software will be unable to create contours for printing. Inverted Normal / / A triangle’s normal is flipped the wrong way which creates an open mesh.
